Blog
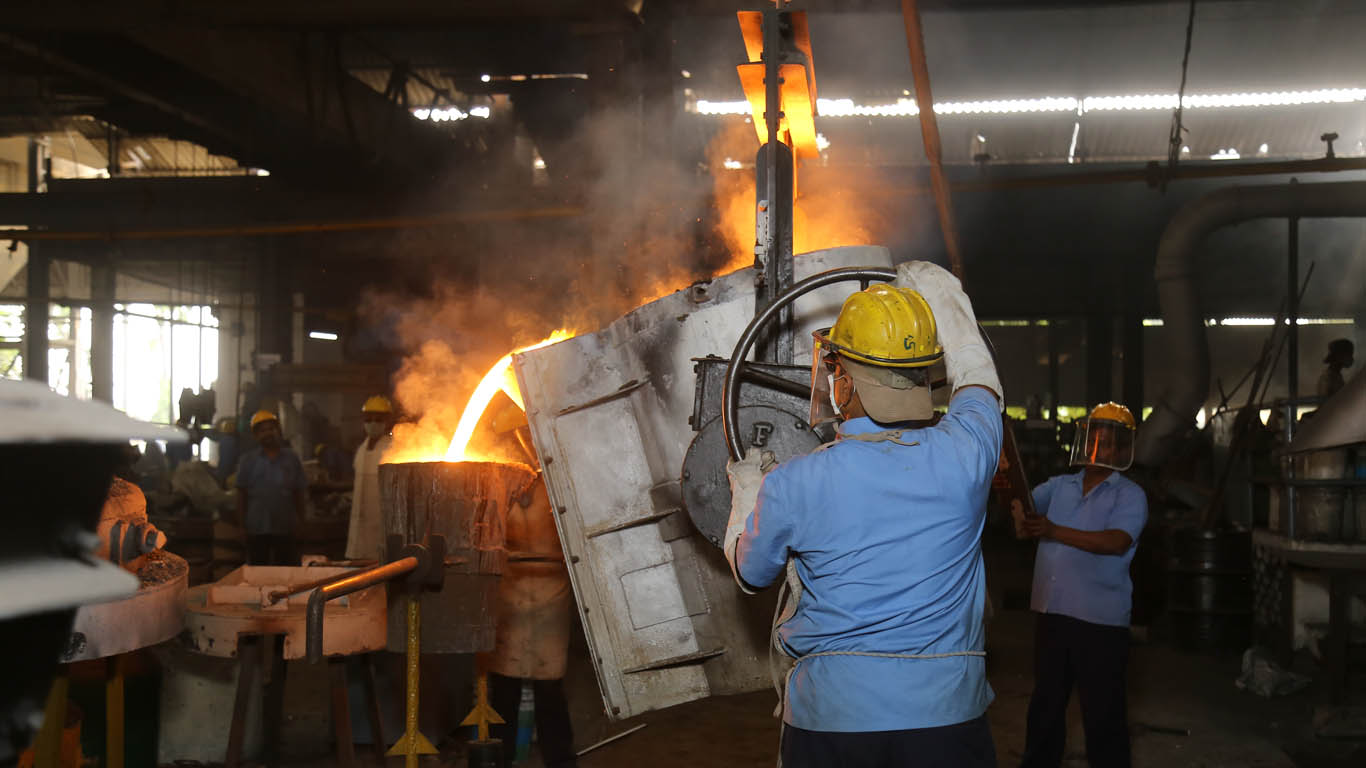
Types of Melting Furnaces Used In Manufacturing Foundries
To make a metal cast, one needs to liquefy the metal first. For metal liquefaction, a foundry needs to have a melting furnace. One of the foremost requirements of any foundry is a melting furnace. Foundries in India and around the globe have witnessed an evolution in the technology of melting furnaces. In this blog, we are going to cover the predominantly used furnaces used in foundries.
Before heading to choose the type of furnace, every foundry must consider the following few factors that influence the decision:
- The alloys that will be used
- The melting point of the alloys
- Quantity of metal to be liquefied and its melting capacity
- The economy of installation and operation of the furnace
- Management of environmental and disposal needs