Blog
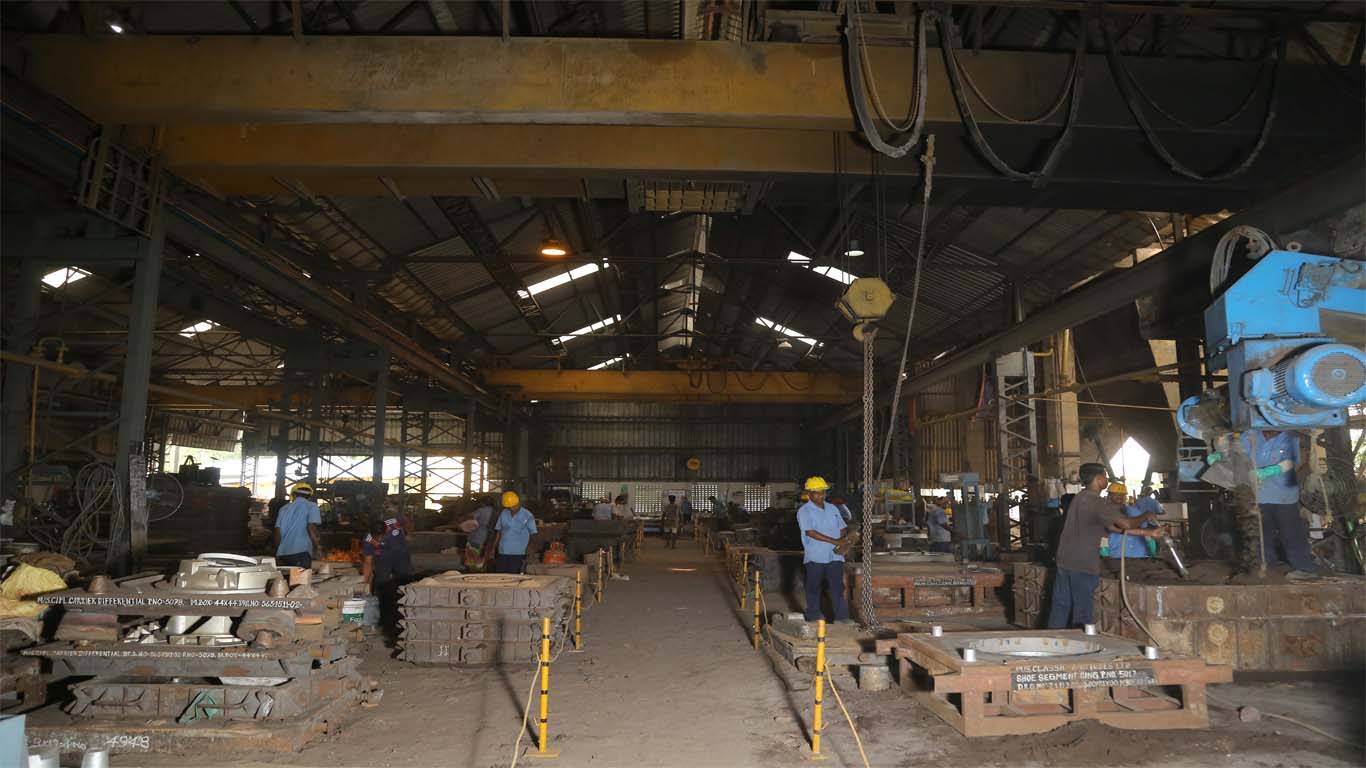
Sand Reclamation In Foundries
All foundries, whether Iron foundries in India or across the globe, use massive quantities of moulding sand. Foundry sand as a raw material raises a degree of concern with regards to handling, transportation, disposal method and the associated costs. The process of moulding sand reclamation in foundries hence gained importance for both economical and environmental reasons.
Sand reclamation is the process of reconditioning or treating spent (used) foundry sand for adhesive binders and coatings (used for casting processes), without compromising its original physical properties. The key factors that affect sand reclamation include resin content, type of sand, type of binder systems, additives and the sand to metal ratio.
The three methods adopted for spent sand reclamation are:
As of January 2020, casting production in India was estimated to be at a whopping 7.4 million tonnes, making us the second-largest producer of grey iron and steel castings. This implies that the foundries in India generate significantly large amounts of toxic, used moulding sand which is unsafe for dumping. All thanks to sand reclamation, we are able to sustainably and economically tackle this issue.
- Mechanical or Cold or Attrition Reclamation:
When a series of mechanical processes are done for spent foundry sand to clean the sand grains off the binders, it is called mechanical reclamation. More often than not, sand reclaimed by this process has to be mixed with 10-20% of new sand as the binders are not removed completely and this mixture can be reused only in the same binder system. - Thermal or Hot Reclamation:
This process involves heating the spent sand at 500 – 900°C in a thermal reclamation system. The system includes equipment such as the lump reducer, pneumatic sand transporter, preheating unit for both sand and air, fluidised bed combustor and cooler, skip hoist and a dust extraction system. This is the most proclaimed method as 100% of the sand is reclaimed and with a higher thermal expansion and other enhanced properties, making it more suitable for casts. Additionally, thermally reclaimed sand can be reused irrespective of the original binder system. SG iron foundries, grey iron foundries and even non-ferrous foundries prefer this method. - Wet Reclamation:
Until the modern dry reclaimers came to use, wet scrubbing was the way for organic core and no-bake sands. Though the interparticle grinding removed the fines efficiently, the resins and binders could not be easily removed off the sand grains.
As of January 2020, casting production in India was estimated to be at a whopping 7.4 million tonnes, making us the second-largest producer of grey iron and steel castings. This implies that the foundries in India generate significantly large amounts of toxic, used moulding sand which is unsafe for dumping. All thanks to sand reclamation, we are able to sustainably and economically tackle this issue.